When you hear about a Russia lathe accident, it might sound like just another industrial mishap, but there’s more to the story than meets the eye. This isn’t just about a machine malfunctioning or human error—it’s a complex mix of factors that highlight the importance of safety protocols, training, and technology in heavy industries. In today’s fast-paced world, accidents like these serve as a wake-up call for everyone involved in manufacturing and engineering.
Let’s break it down real quick. A lathe machine is basically a badass piece of equipment used to shape metal, wood, or other materials by rotating them against a cutting tool. It’s one of those workhorses in factories worldwide, but when things go wrong, they go *really* wrong. Russia has been no stranger to industrial accidents over the years, but this particular incident caught everyone’s attention because of its severity and the lessons it holds.
Before we dive deep into the nitty-gritty, let’s set the stage. The Russia lathe accident wasn’t just an isolated event; it was a reflection of broader issues in industrial safety across the globe. From poorly maintained machinery to inadequate training, there’s a lot to unpack here. So buckle up, because we’re about to take you through the ins and outs of what happened, why it matters, and how we can prevent similar incidents in the future.
Read also:Son And Mom Cctv The Untold Stories Captured On Camera
Understanding the Role of Lathes in Modern Manufacturing
To truly grasp the significance of the Russia lathe accident, you gotta understand how lathes work and their role in modern manufacturing. These machines are like the backbone of many industries, responsible for creating everything from tiny screws to massive engine parts. They’ve been around for centuries, but with advancements in technology, they’ve become more precise, efficient, and, yes, potentially more dangerous if not handled properly.
Here’s the deal: lathes are powerful tools that require skill and precision. A single mistake can lead to catastrophic consequences, not just for the operator but for the entire production line. In Russia, where manufacturing plays a huge role in the economy, the reliance on these machines is immense. But with great power comes great responsibility, and sometimes, that responsibility gets overlooked.
How Lathes Work: A Simplified Explanation
Now, let’s talk about the basics. A lathe operates by spinning the material (usually metal) against a cutting tool. The operator controls the speed, feed, and depth of the cut, ensuring the final product meets the desired specifications. Sounds simple enough, right? Well, here’s the catch: even the slightest miscalculation can result in a major accident. That’s why proper training and safety measures are crucial.
Imagine this: you’re working with a lathe that’s been running nonstop for hours. The machine starts to overheat, but instead of shutting it down for maintenance, you push through because there’s a deadline to meet. Suddenly, the tool slips, and before you know it, you’ve got a serious problem on your hands. This scenario might sound dramatic, but it’s closer to reality than you think.
What Happened in the Russia Lathe Accident?
The Russia lathe accident was no ordinary mishap. It involved a combination of factors that led to a perfect storm of disaster. While the exact details may vary depending on the source, the general consensus is that a combination of human error, outdated equipment, and lack of proper safety protocols played a significant role.
According to reports, the accident occurred in a factory located in one of Russia’s industrial hubs. The lathe in question was reportedly old and in need of maintenance, but instead of addressing the issue, the management decided to keep it running to avoid production delays. Sound familiar? This kind of decision-making is unfortunately all too common in industries where profit often takes precedence over safety.
Read also:Unveiling The Original Four Girls Fingerprint Video A Deep Dive
Key Factors That Contributed to the Accident
- Outdated Machinery: The lathe involved in the accident was reportedly over 20 years old, with no recent upgrades or maintenance checks.
- Lack of Training: The operator was allegedly inadequately trained, which increased the risk of errors during operation.
- Pressure to Meet Deadlines: The factory was under immense pressure to meet production targets, leading to shortcuts in safety procedures.
- Inadequate Safety Measures: Basic safety protocols, such as regular machine inspections and operator certification, were reportedly neglected.
These factors combined to create a recipe for disaster. When the lathe finally gave way, the consequences were severe, resulting in injuries and significant downtime for the factory. It’s a stark reminder that cutting corners in safety is never worth the risk.
Who Was Affected by the Accident?
When an accident like this happens, the impact is felt far beyond the immediate victims. In the case of the Russia lathe accident, several groups were affected, from the workers on the ground to the factory owners and even the local community.
First and foremost, the workers involved in the accident suffered the most. Injuries ranged from minor cuts to severe trauma, depending on how close they were to the machine when it malfunctioned. For some, this meant time off work and medical bills piling up. For others, it meant the end of their careers in manufacturing altogether.
The Ripple Effect on the Community
But it didn’t stop there. The factory’s downtime had a ripple effect on the local economy. Suppliers who relied on the factory for business saw orders dry up, while workers who were laid off struggled to make ends meet. The community as a whole felt the weight of the accident, highlighting the interconnectedness of modern industries.
And let’s not forget the psychological impact. Accidents like these leave lasting scars, not just on the victims but on their families and colleagues as well. The fear of returning to work after such an incident can be paralyzing, leading to a decline in morale and productivity.
What Can We Learn from the Russia Lathe Accident?
Every accident is an opportunity to learn, and the Russia lathe accident is no exception. By examining what went wrong, we can identify areas for improvement and take steps to prevent similar incidents in the future.
One of the key lessons here is the importance of regular maintenance. Machines, no matter how durable they seem, need regular check-ups to ensure they’re functioning properly. This isn’t just about extending the lifespan of the equipment; it’s about protecting the people who use it.
Investing in Training and Technology
Another takeaway is the need for proper training. Operators should be well-versed in the latest safety protocols and equipped with the skills to handle modern machinery. This might require additional investment in training programs, but it’s a small price to pay for preventing accidents.
Technology also plays a crucial role in improving safety. Modern lathes come equipped with advanced sensors and monitoring systems that can detect potential issues before they become serious problems. Investing in these technologies can save lives and money in the long run.
Steps to Prevent Future Accidents
So, what can factories and manufacturers do to prevent future accidents? Here are a few actionable steps:
- Regular Maintenance: Schedule routine inspections and maintenance checks for all machinery.
- Comprehensive Training: Provide ongoing training for operators to keep them up-to-date with the latest safety practices.
- Invest in Technology: Upgrade to modern equipment with built-in safety features whenever possible.
- Foster a Safety Culture: Encourage a workplace culture where safety is prioritized over profit.
Implementing these steps might require some upfront costs, but the benefits far outweigh the risks. After all, a safe workplace is a productive workplace.
Industry Standards and Regulations
It’s worth noting that there are industry standards and regulations in place to ensure safety in manufacturing environments. These guidelines are designed to protect workers and minimize the risk of accidents, but they’re only effective if they’re followed.
In Russia, as in many other countries, there are strict regulations governing the use of industrial machinery. However, enforcement can sometimes be lacking, especially in smaller factories where resources are limited. This highlights the need for greater oversight and accountability in the industry.
The Role of Government and Oversight Bodies
Governments and oversight bodies have a crucial role to play in ensuring compliance with safety regulations. Regular audits and inspections can help identify potential hazards before they lead to accidents. Additionally, penalties for non-compliance can act as a deterrent for factories that prioritize profit over safety.
But it’s not just about enforcing rules; it’s about creating a culture of safety that permeates every level of the organization. This requires collaboration between government agencies, industry leaders, and workers themselves.
Case Studies: Similar Accidents Around the World
The Russia lathe accident isn’t the first of its kind, nor will it be the last. Similar incidents have occurred in other parts of the world, each with its own set of circumstances and lessons to learn.
For example, in 2019, a lathe accident at a factory in India resulted in the death of two workers. The investigation revealed that the machine had not been properly maintained, and the operators were inadequately trained. Sound familiar? It’s a stark reminder that these issues aren’t unique to Russia; they’re a global concern.
Learning from Others’ Mistakes
By studying these case studies, we can gain valuable insights into what works and what doesn’t when it comes to preventing industrial accidents. Sharing best practices and lessons learned can help create a safer working environment for everyone involved.
It’s also worth noting that technology plays a crucial role in these case studies. Factories that have invested in modern equipment and safety systems tend to have fewer accidents, highlighting the importance of staying up-to-date with the latest advancements.
Conclusion: Taking Action for a Safer Future
In conclusion, the Russia lathe accident serves as a powerful reminder of the importance of safety in manufacturing environments. From outdated machinery to inadequate training, there are many factors that contribute to these types of incidents. But by learning from our mistakes and taking proactive steps to improve safety, we can prevent future accidents and create a safer working environment for everyone.
So, what can you do? If you’re a factory owner or manager, invest in regular maintenance, comprehensive training, and modern technology. If you’re a worker, speak up about safety concerns and advocate for better practices. And if you’re a member of the community, support initiatives that prioritize safety over profit.
Together, we can make a difference. Share this article with your network, leave a comment with your thoughts, and let’s start a conversation about creating a safer future for all.
Table of Contents
- Russia Lathe Accident: A Closer Look at What Happened and the Lessons We Can Learn
- Understanding the Role of Lathes in Modern Manufacturing
- How Lathes Work: A Simplified Explanation
- What Happened in the Russia Lathe Accident?
- Key Factors That Contributed to the Accident
- Who Was Affected by the Accident?
- The Ripple Effect on the Community
- What Can We Learn from the Russia Lathe Accident?
- Investing in Training and Technology
- Steps to Prevent Future Accidents
- Industry Standards and Regulations
- The Role of Government and Oversight Bodies
- Case Studies: Similar Accidents Around the World
- Learning from Others’ Mistakes
- Conclusion: Taking Action for a Safer Future

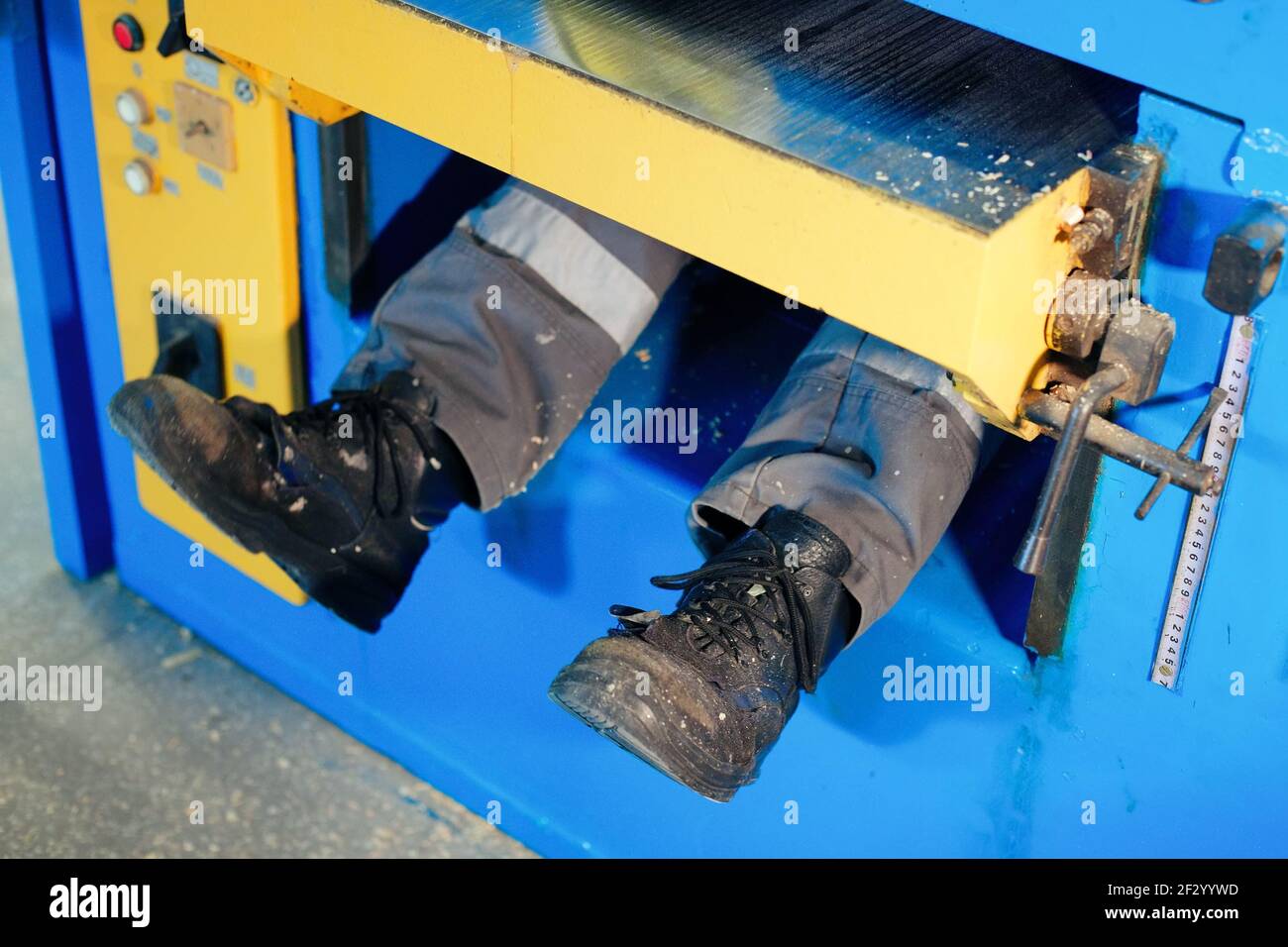
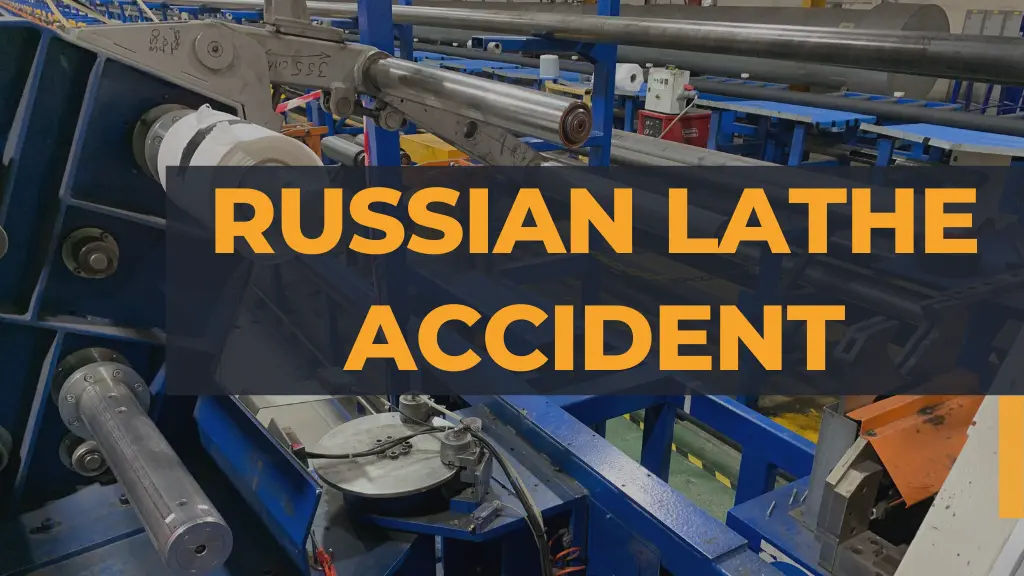